重要日期
- 截止日期: 2019年7月8日
- 录用通知: 投稿后20-40天
- 论文出版: 收到最终稿后15-20天
- 会议日期: 2019年8月12-14日
联系我们
-
huiyi123net_Aug@126.com
-
021-51098086
-
0086-18101720867
-
18101720867
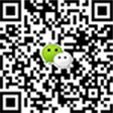
WCEESD2019演讲嘉宾信息如下:
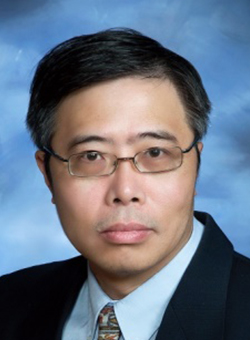
Biography: Dr. Hongfa Hu is a tenured full Professor at Department of Mechanical, Automotive & Materials Engineering, University of Windsor. He was a senior research engineer at Ryobi Die Casting (USA), and a Chief Metallurgist at Meridian Technologies, and a Research Scientist at Institute of Magnesium Technology. He received degrees from University of Toronto (Ph.D., 1996), University of Windsor (M.A.Sc., 1991), and Shanghai University of Technology (B.A.Sc., 1985). He was a NSERC Industrial Research Fellow (1995-1997). His publications (over 150 papers) are in the area of magnesium alloys, composites, metal casting, computer modelling, and physical metallurgy. He was a Key Reader of the Board of Review of Metallurgical and Materials Transactions, a Committee Member of the Grant Evaluation Group for Natural Sciences and Engineering Research Council of Canada, National Science Foundation (USA) and Canadian Metallurgical Quarterly. He has served as a member or chairman of various committees for CIM-METSOC, AFS, and USCAR. The applicant’s current research is on materials processing and evaluation of light alloys and composites. His recent fundamental research is focussed on transport phenomena and mechanisms of solidification, phase transformation and dissolution kinetics. His applied research has included development of magnesium automotive applications, cost-effective casting processes for novel composites, and control systems for casting processes. His work on light alloys and composites has attracted the attention of several automotive companies.
Topic: Light Weight Mg Alloys for Energy-Efficient Auto Applications: Properties and Microstructure
Abstract: The use of magnesium in the automotive industry has grown dramatically in response to consumer demands for increased performance and fuel economy of vehicles. Mg alloys currently used in the automotive industry are high-pressure die cast (HPDC), and have either relatively good strengths or high ductility at room temperature. Applications of HPDC magnesium alloys include front end support assemblies, steering wheel armatures and steering column support brackets, which have cross sections with difference thicknesses and complex shapes. Section thickness is an easily measured parameter for comparing various castings. During the HPDC production, thick sections have a higher tendency to form solidification shrinkage and porosity caused by inclusion of gas than thin walls. AZ91, as one the most popular magnesium alloys is widely used for various engineering applications in the automotive industry. They are primarily made from high pressure die cast processes (HPDC) with different cross-section thicknesses, which affect their engineering performance. Understanding the effect of section thicknesses on mechanical behaviors of HPDC AZ91 is crucial for proper design of lightweight components to meet desired engineering requirement. In the present study, magnesium alloy AZ91 was high pressure die cast into rectangular coupons with section thicknesses of 2, 6 and 10 mm. The prepared coupons were tensile tested at room temperature. Microstructure analysis and porosity measurement were performed on the representative specimens. The results of tensile testing show that the tensile properties including yield strength (YS), ultimate tensile strength (UTS) and elongation (Ef) decreases with an increase in section thicknesses of die cast AZ91. Microstructure and porosity analyses indicate that the observed tensile behavior of die cast AZ91 is primarily attributed to the level of porosity which results from gases entrapped during the HPDC process.
© 2016-2019第三届能源,环境与可持续发展大会 版权所有